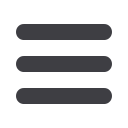
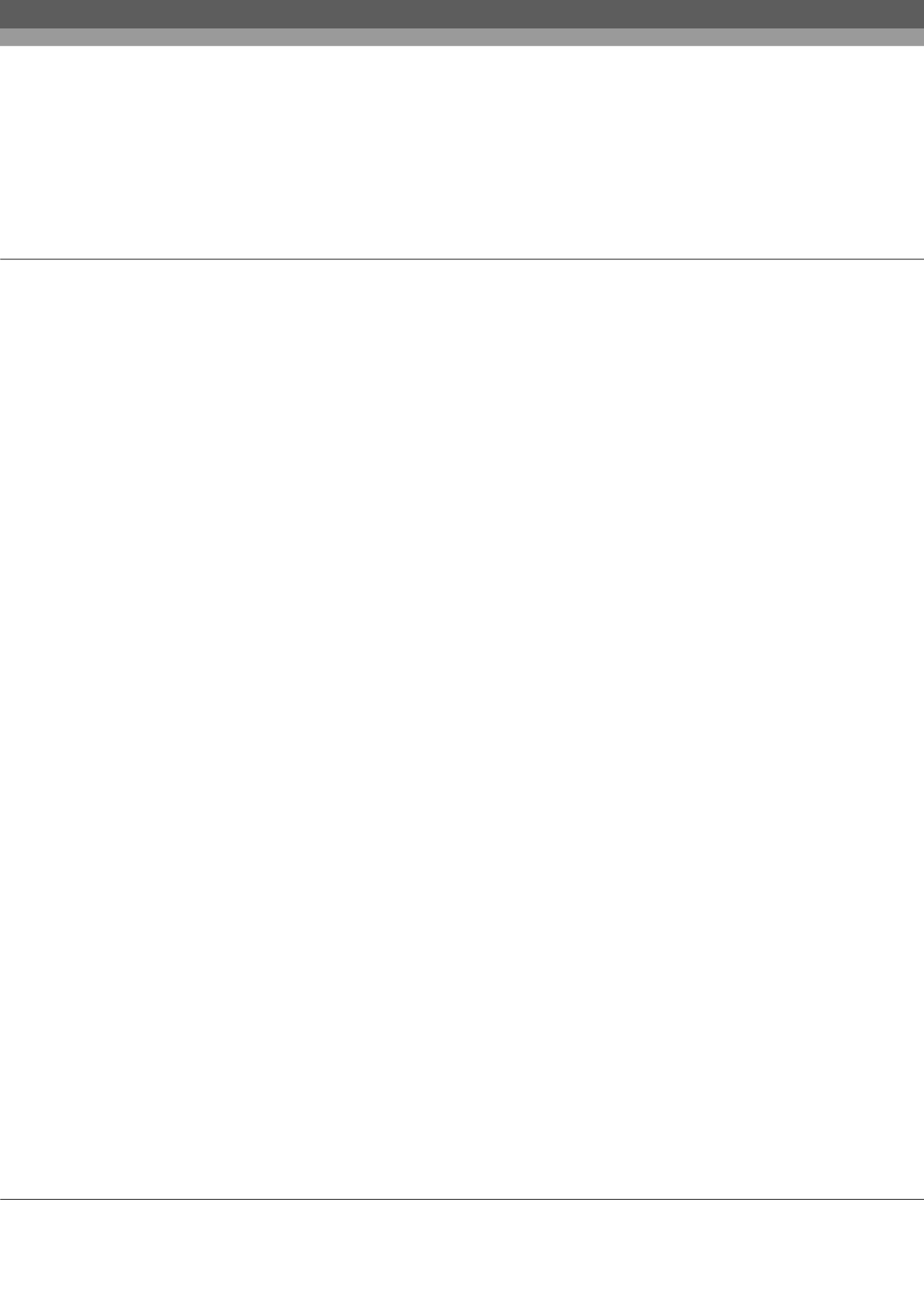
Notes:
Volume 6, Issue 4 (Suppl)
Clin Pharmacol Biopharm, an open access journal
ISSN: 2167-065X
Page 51
Euro Biopharma & Ethnopharmacology 2017
November 09-11, 2017
&
6
th
International Conference and Exhibition on
November 09-11, 2017 Vienna, Austria
4
th
EUROPEAN BIOPHARMA CONGRESS
PHARMACOLOGY AND ETHNOPHARMACOLOGY
Joint Event
Achieving Quality by Design for parenterals filling with a time-pressure setup
Yannick Elias
Janssen (Cilag AG), Switzerland
P
articulate matter in parenteral drug products is recognized by Health Authorities as a critical quality attribute. A strong focus of fill
and finish process development is put on the appropriate selection and operation of the filling system to reduce intrinsic particle
formation, often related to shear induced drug product degradation. Rotary Piston Pumps (RPP) have been a standard selection in
Janssen for many years, as they offer a simple, compact and robust design and show a very high dosing accuracy. However, as the
drug product acts as a pump lubricant, the product is exposed to very high shear rates, which in turn can cause enhanced intrinsic
particle formation. Thus, alternative filling technologies, such as peristaltic pumps (PP) or a time-pressure (TP) system, are required
for shear-sensitive products. A TP system consists essentially of a pressurized tank and a pinch valve. Dosing accuracy is achieved by
harmonizing the vessel over pressure and the valve opening duration. To improve the overall product quality during filling of shear-
sensitive products, a Quality by Design and Right the First Time approach is chosen to ensure proper equipment operation. For this,
understanding the critical process parameters, risks associated with those parameters and their impact on critical product quality
attributed is crucial. Thus, a Design of Experiment study was performed to identify and characterize the impact of six distinct process
and equipment parameters on different solutions to obtain a Design Space for optimal TP filling operation.
Biography
Yannick Elias completed his PhD from Swiss Federal Institute of Technology Zurich (ETH Zürich) in Process Engineering, focusing on continuous heterogonous
reactions and has published several papers in reputed journals. Currently, he works for Janssen Pharmaceutical Development and Manufacturing Sciences
(PDMS) as a Process Engineer, focusing on development for parenterals fill and finish operations. He worked with Janssen for more than one and a half years and
is currently leading the strategic expansion of a large molecule drug product development laboratory.
yelias@its.jnj.comYannick Elias, Clin Pharmacol Biopharm 2017, 6:4(Suppl)
DOI: 10.4172/2167-065X-C1-025