
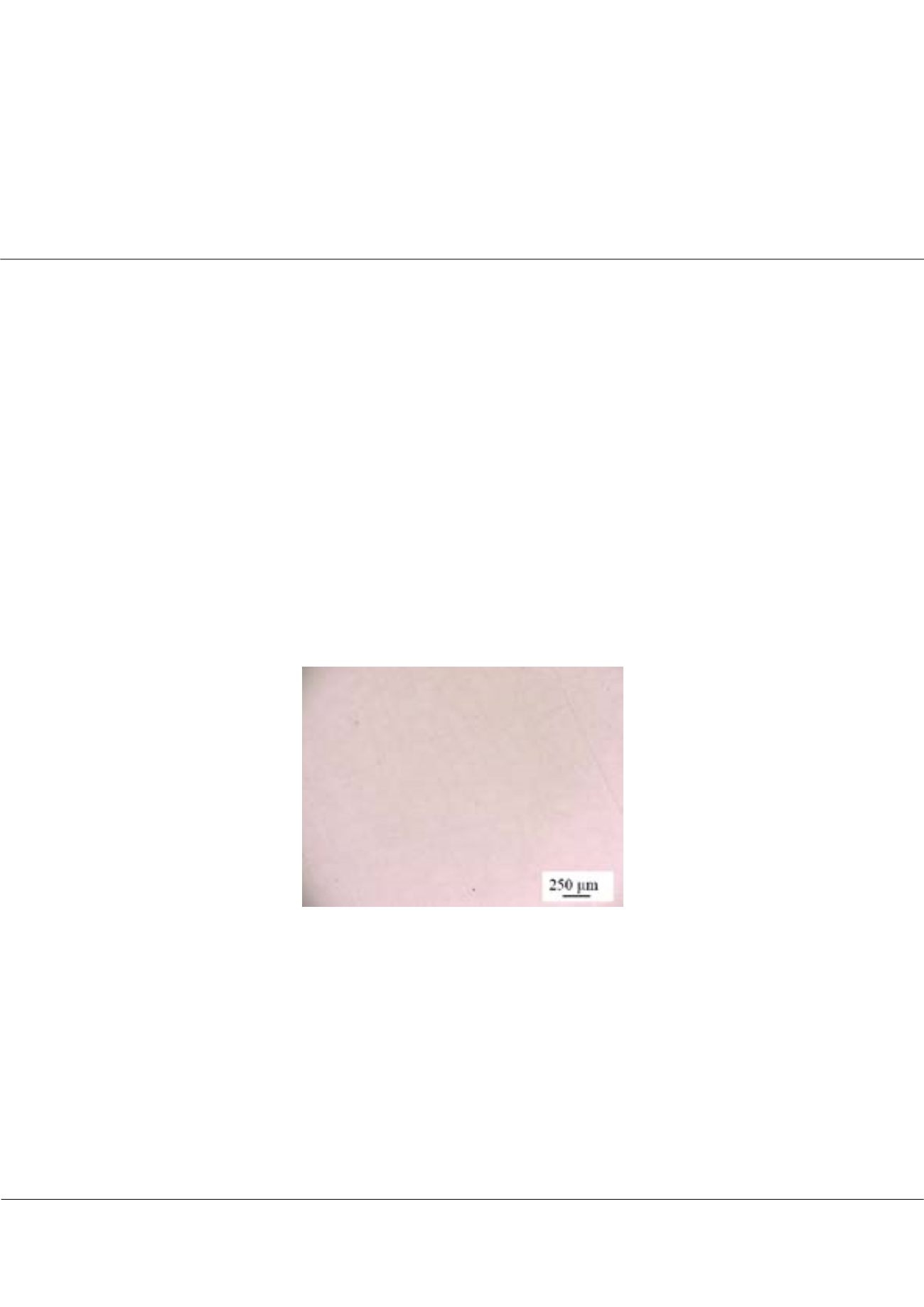
Page 67
conferenceseries
.com
Volume 9
International Journal of Advancements in Technology
ISSN: 0976-4860
3D Printing 2018
March 19-20, 2018
March 19-20, 2018 | London, UK
2
nd
International Conference on
3D Printing Technology and Innovations
Selective laser melting of a new tailored aluminium alloy (SilmaAl® AlSi7Mg0.6) for aerospace
industry
Camilo Zopp
1
, Frank Schubert
1
, Frank Palm
2
, Hubertus Lohner
2
, Freerk Syassen
2
and
Lothar Kroll
1
1
Chemnitz University of Technology, Germany
2
Airbus Central Research & Technology (CRT), Airbus, Ottobrunn, Europe, Germany
I
n recent years the demand for additive manufactured components has experienced a considerable boost due to increased
technical, economic and geometrical requirements. Above all for the aerospace industry, the additive production technology
is predestined for the production of tailor-made and geometrically complex components. In particular, laser powderbed fusion
(LPB-F) is characterized as an innovative and directional production process with enormous potential. Aluminum alloys are
excellent lightweight materials due to their comparatively high stiffness and strength combined with low weight. However,
the current use in the additive production process is limited by the comparatively difficult processing and which can lead to
undesired low material densities. The focus of the work was the development of suitable LPB-F process parameters for higher
strength and low oxygen aluminum alloy AlSi7Mg0.6 (SilmagAl®). In this context, material densities of approx. 99.98 % could
be achieved. In the second step, mechanical investigations were carried out under static load. A comprehensive trade-off
and comparison was made between different heat treatments. In the static range, yield stresses of up to 300 MPa and tensile
strengths of up to 430 MPa have been achieved. The fracture elongation at break could be adjusted accordingly with values
up to 20%. Hence processing of this improved aluminum alloy and the generated mechanical properties, new application
potentials in the aerospace sector will open up, e.g. for future hydraulic components.
Biography
Camilo Zopp graduated in Mechanical Engineering studies at Dresden University of Technology, Germany in 2013. Since 2014, he is a Research Assistant in the
Department of Mechanical Engineering at Chemnitz University of Technology, Germany. He is currently working in the Germany’s first and only Federal Cluster of
Excellence “MERGE” in the field of lightweight structures. His research focuses on additive manufacturing, selective laser melting (SLM) especially in processing
of new materials and development of material parameters. Another research topic is the production of thermoplastic-based hybrid laminates. He is in interested in
the processing of new metal alloys and development of design guidelines.
camilo.zopp@mb.tu-chemnitz.deCamilo Zopp et al., Int J Adv Technol 2018, Volume 9
DOI: 10.4172/0976-4860-C1-002
Figure 1:
Material density of AlSi7Mg0.6.