
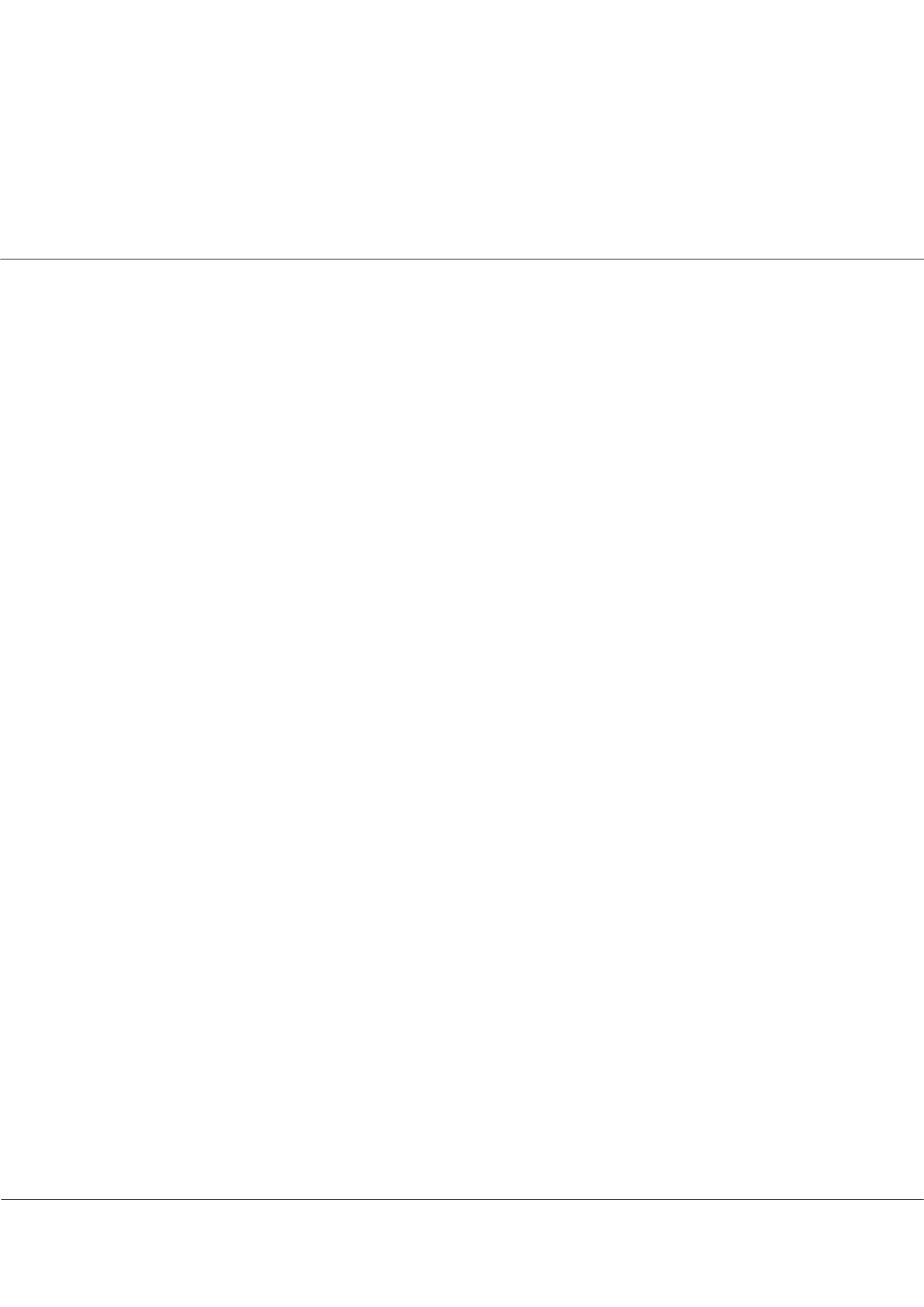
Page 65
Notes:
conferenceseries
.com
Volume 9
International Journal of Advancements in Technology
ISSN: 0976-4860
3D Printing 2018
March 19-20, 2018
March 19-20, 2018 | London, UK
2
nd
International Conference on
3D Printing Technology and Innovations
Advanced materials and technologies in aviation industry
Tomasz Kurzynowski, Wojciech Stopyra
and
Andrzej Pawlak
Wroclaw University of Science and Technology, Poland
A
dditive Manufacturing (3D printing) offers the possibility of producing individually designed products that perfectly
fulfill their functions – even the most complex ones. AM uses layered production techniques to produce functional
finished parts. This process facilitates building of a part frommaterials that are difficult to machine and enables the production
of complex parts for demanding industries such as aerospace. This direction of AM technology development is related to
the ability of producing any geometric structure and to use a wide range of processing materials, including typical “aerial”
materials used to reduce mass, such as aluminum, magnesium and titanium alloys. It clearly shows the growing impact on the
cost of two main factors: 1. use increasingly advanced and expensive materials and 2. technological, construction and assembly
work. The use of magnesium for aviation applications is an opportunity to meet the high requirements and mass reduction
of parts. The density of magnesium (1.77 g/cm
3
) is almost twice as low as conventional aluminum (2.77 g/cm
3
). Considering
mechanical properties of magnesium (E=34 GPa, hardness 0.6-0.95 GPa), it is characterized by excellent strength-to-weight
ratio (specific strength). This is the reason why in advanced areas of industry where the mass of products is crucial, magnesium
alloys are the desired materials. Additive technologies (AMs) processing metals, plastics and composites that are currently in
advanced development stage (or even commercially availabe) may have a huge impact on the cost of aircraft components by
reducing the “buy-to-fly” ratio and eliminating some production, assembly and logistics activities. This is closely related to the
capabilities of additive technologies, including: 1. the ability to create extremely complex shapes, spatial internal structures,
etc., which reduce the weight of a product by up to 50% compared to conventional methods. 1. the possibility of producing one
component that replaces a functional collection of several or even a dozen components made using traditional methods. 2. raw
material savings – the amount of material needed (e.g. titanium or aluminum alloy) is only slightly larger than the volume of
produced parts; additive technologies do not generate material waste as opposed to traditional technologies like machining,
where losses can reach as much as 90% of the input material.
Biography
Tomasz Kurzynowski completed his PhD 6 years ago from the Wroclaw University of Science and Technology, Poland and a professional development program
from the Stanford University, USA. He is the Manager of Metal Additive Manufacturing Technology and Materials Laboratory, a Member of the Board of the Science
Infrastructure Management Society. He has published more than 20 papers in reputed journals and over 150 industrial experises. His current research interest
include additive manufacturing technologies and design methods for functional optimization or weight reduction of designed or reengineered parts, especially for
the aerospace industry..
tomasz.kurzynowski@pwr.edu.plTomasz Kurzynowski et al., Int J Adv Technol 2018, Volume 9
DOI: 10.4172/0976-4860-C1-002