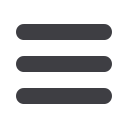
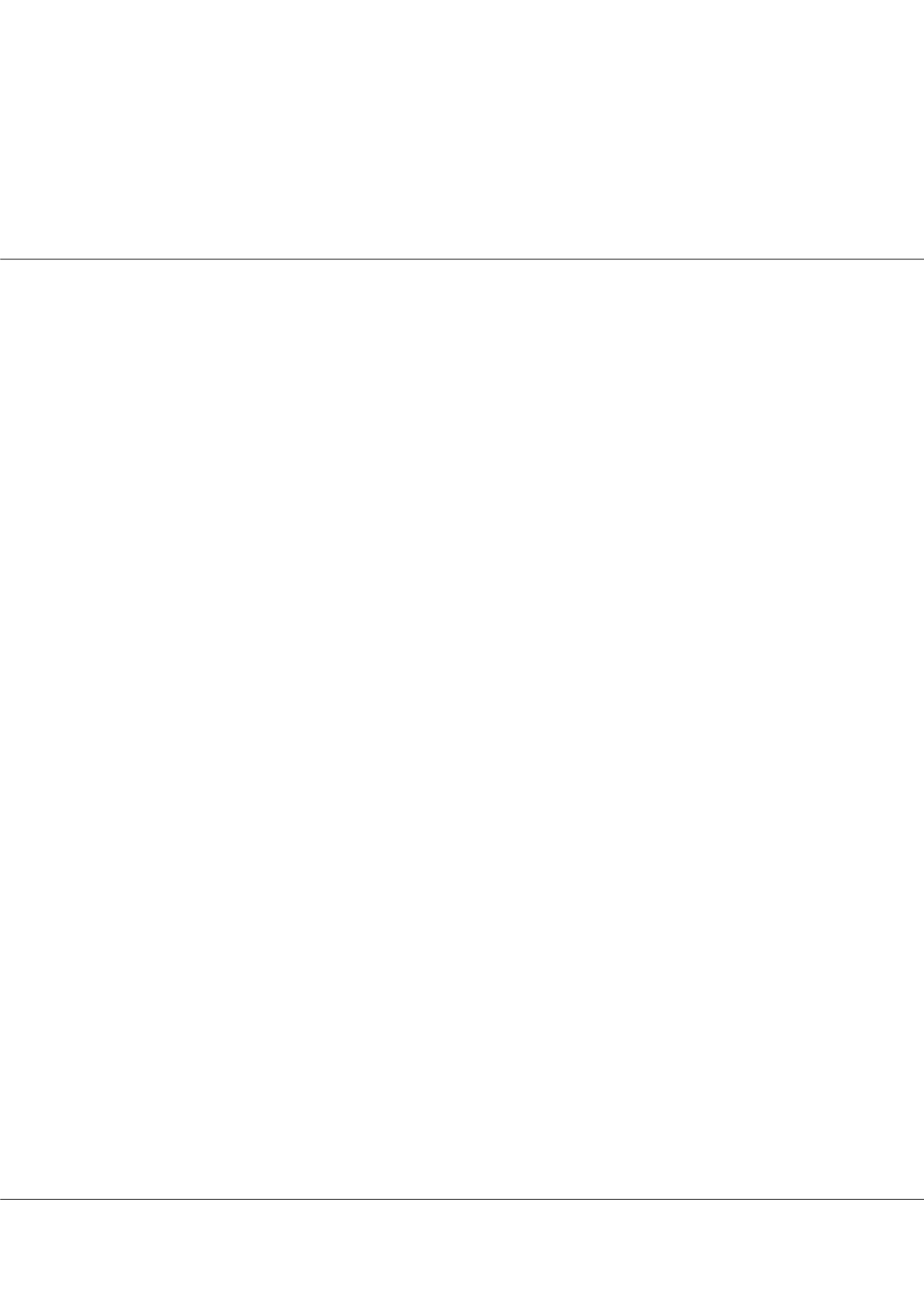
Page 39
Notes:
conferenceseries
.com
March 20-22, 2017 Orlando, USA
3
rd
International Conference on
Smart Materials & Structures
Volume 6, Issue 2 (Suppl)
J Material Sci Eng
ISSN: 2169-0022 JME, an open access journal
Smart Materials 2017
March 20-22, 2017
Mechanics based design and testing of crack closing self-healing materials to carry external loads
Nathan P Salowitz, Ameralys Correa, Afsaneh Moghadam
and
Pradeep Rohatgi
University of Wisconsin-Milwaukee, USA
S
elf-healingmaterials have innate capabilities to restore geometry andmend damage in a structure.Thesematerials have tremendous
potential to prevent catastrophic failures and overcome fatigue issues by repairing structural damage as it occurs, while in service.
In order to restore bulk deformations and close macroscopic cracks self-healing materials have been developed that are essentially
sparse fiber composites, composed of a structural matrix reinforced with shape memory fibers. This composition is capable of closing
large cracks and restoring bulk geometry in a free, unloaded state. A significant limitation of this technique is that structures are not
capable of overcoming or withstanding externally applied loads while restoring their original geometry. This is because the shape
memory material used to restore geometry is currently cast in its trained geometry. Therefore, activation and recovery will only
provide loads to return to that original geometry, negating plastic deformation of the matrix and any externally applied load will
cause deviation, inhibiting geometric restoration. Seeking to overcome this limitation, polymer samples were created containing
prestrained nickel titanium shape memory fibers that undergo constrained recovery upon activation. Actuation of the shape memory
fibers generates internal/residual loads allowing the healed structure to withstand and overcome externally applied loads. Theory,
experimental results, analysis and future vision for self-healing materials composed of prestrained nickel titanium shape memory
fibers are discussed. A mechanics based derivation is presented relating internal/residual loads to allowable externally applied loads.
Experimental results are presented from samples composed of prestrained shape memory alloy reinforced polymer with an internal
framework to ensure load transfer between components. Samples were loaded in tension with a constant crosshead speed until matrix
failure, then healed through thermal actuation and loaded to crack opening multiple times. Analysis of theory and experimental
results are presented.
Biography
Nathan P Salowitz has received his BS degree in Engineering Mechanics from the University of Wisconsin Madison in 2001 and MS and PhD degrees in
Aeronautics and Astronautics from Stanford University in 2006 and 2013, respectively. From 2003 to 2005, he was a Structural Analysis Engineer with The Boeing
Company. From 2013 to 2014, he was a Postdoctoral Engineering Research Associate at Stanford University. Since 2014, he has been an Assistant Professor with
the Mechanical Engineering Department with Adjunct Professor Appointments in the Electrical Engineering and Civil and Environmental Engineering departments
at the University of Wisconsin-Milwaukee. He has more than 16 publications and is currently pursuing research in intelligent materials and structural health
monitoring with particular interests in sensor design, mass sensor deployment, wireless communication and the interaction of sensors and structures.
Salowitz@UWM.eduNathan P Salowitz et al., J Material Sci Eng 2017, 6:2 (Suppl)
http://dx.doi.org/10.4172/2169-0022.C1.061