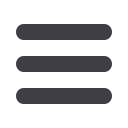
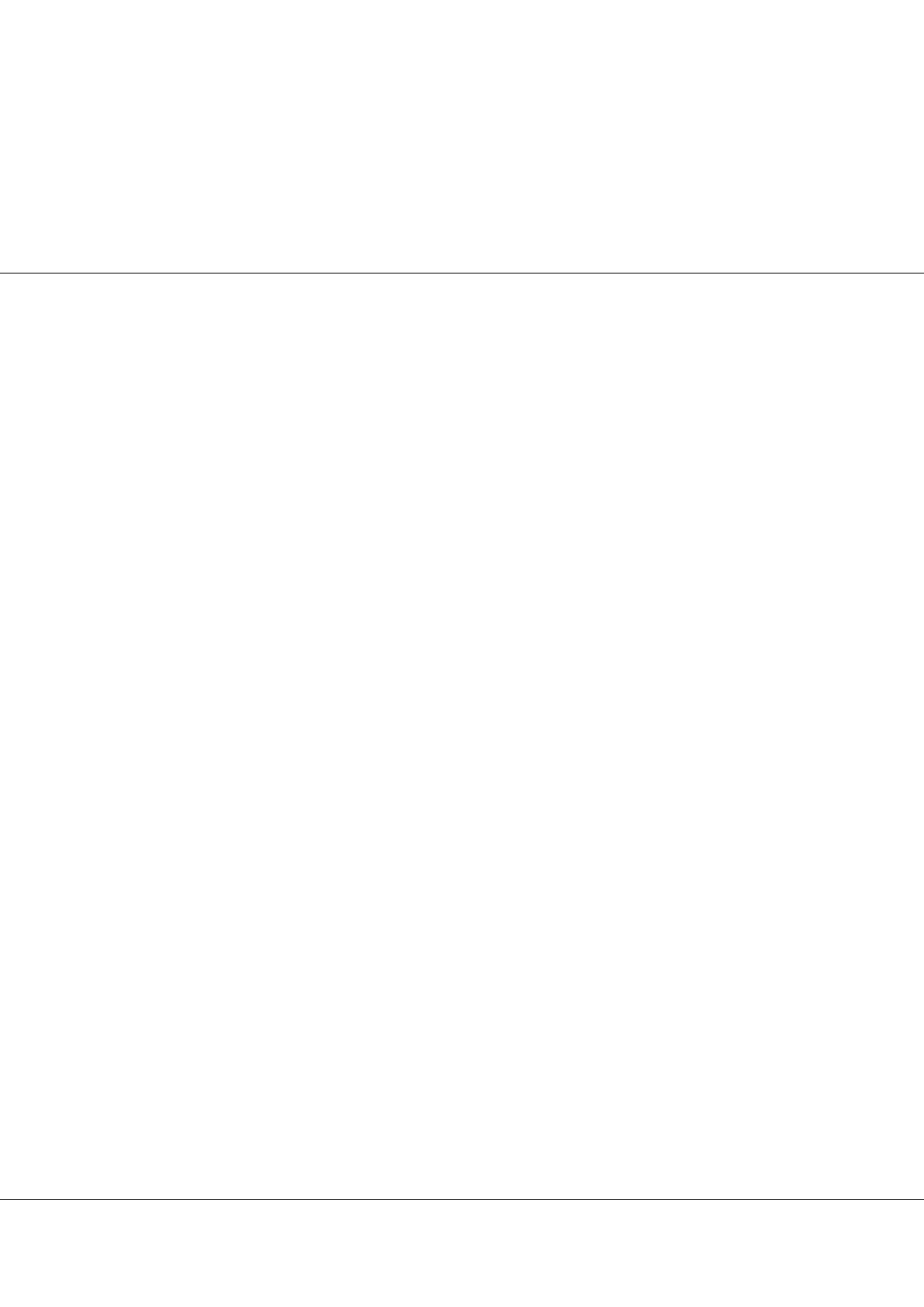
Volume 5, Issue 2(Suppl)
Adv Automob Eng 2016
ISSN: 2167-7670, AAE an open access journal
Page 37
Notes:
Automobile 2016
December 01-02, 2016
conferenceseries
.com
Automobile Engineering
December 01-02, 2016 Valencia, Spain
2
nd
International Conference and Exhibition on
Influence of operating factors on modal characteristics of a rolling truck tyre
Subhash Rakheja, Shahram Shokouhfar
and
A K W Ahmed
Concordia University, Canada
A
structural 3D tyre model is developed for estimating modal characteristics of a rolling truck tyre using LS-DYNA finite element
analysis platform. The model takes into account the complex construction of a pneumatic tyre such as the multi-layered
composite designs of carcass and belts as well as hyper-elastic rubber materials forming the tread and bead fillers. The validity of
the structural tyre model was thoroughly examined via comparisons with reported experimental data in view of vertical and lateral
forces, and aligning moment characteristics. The verified tyre model is subsequently employed to study its modal characteristics in
terms of variations in vibration modes and frequencies of the pre-loaded pneumatic tyre structure considering ranges of loading
conditions such as inflation pressure, normal load and rolling speed. The influences of these loading conditions are incorporated
in the eigenvalue calculations via applying the large-deformation finite element theory, where a new term, known as the geometric
stiffness matrix, is introduced to the material stiffness matrix of the system. This new term accounts for nonlinear geometric effects
due to rotations of stresses arising from the loading conditions. A number of prior explicit dynamic simulations are thus necessitated
in order to determine the stress state throughout the tyre model at circumstances when the modal characteristics are desired. This
is achieved using LS-DYNA via the intermittent eigenvalue extractions during an explicit dynamic simulation at three distinct
instants including: (i) Following tyre inflation in response to the internal pressure under given loading condition; (ii) following
steady-state tyre deflection due to applied normal load; and (iii) following a given steady rolling speed. These permitted the analyses
of variations in modal frequencies and deflection modes under applied inflation pressure, loading and rolling speed. The validity
of the simulation results are established through demonstrating correlations of predicted natural modes and frequencies with the
reported data for similar tyres. Furthermore, a computationally efficient algorithm is formulated and applied to facilitate model
reformulations for parametric studies. The results showed significant contributions of all the operating factors considered, namely,
inflation pressure, vertical load and rolling speed. Several pairs of conjugate mode frequencies were further detected for the inflated
tyre due to symmetry. For the deflected tyre, however, each pair diverged to two distinct frequencies with one lower and other higher
than the corresponding frequency of the tyre under inflation alone.
Biography
Subhash Rakheja is a professor of mechanical engineering at the CONCAVE Research Center, Concordia University, Montreal, Canada. He is a research chair in vehicular
ergo-dynamics in Concordia University. Dr. Rakheja is a fellow of the CSME and of the ASME. He is the editor of the International Journal of Industrial Ergonomics and
associate editor of the SAE Journal of Commercial Vehicles and International Journal of Heavy Vehicle Systems. He continues to serve in the Canadian Advisory Council
on International Standards.
subhash.rakheja@concordia.caSubhash Rakheja et al., Adv Automob Eng 2016, 5:2(Suppl)
http://dx.doi.org/10.4172/2167-7670.C1.005