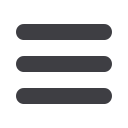
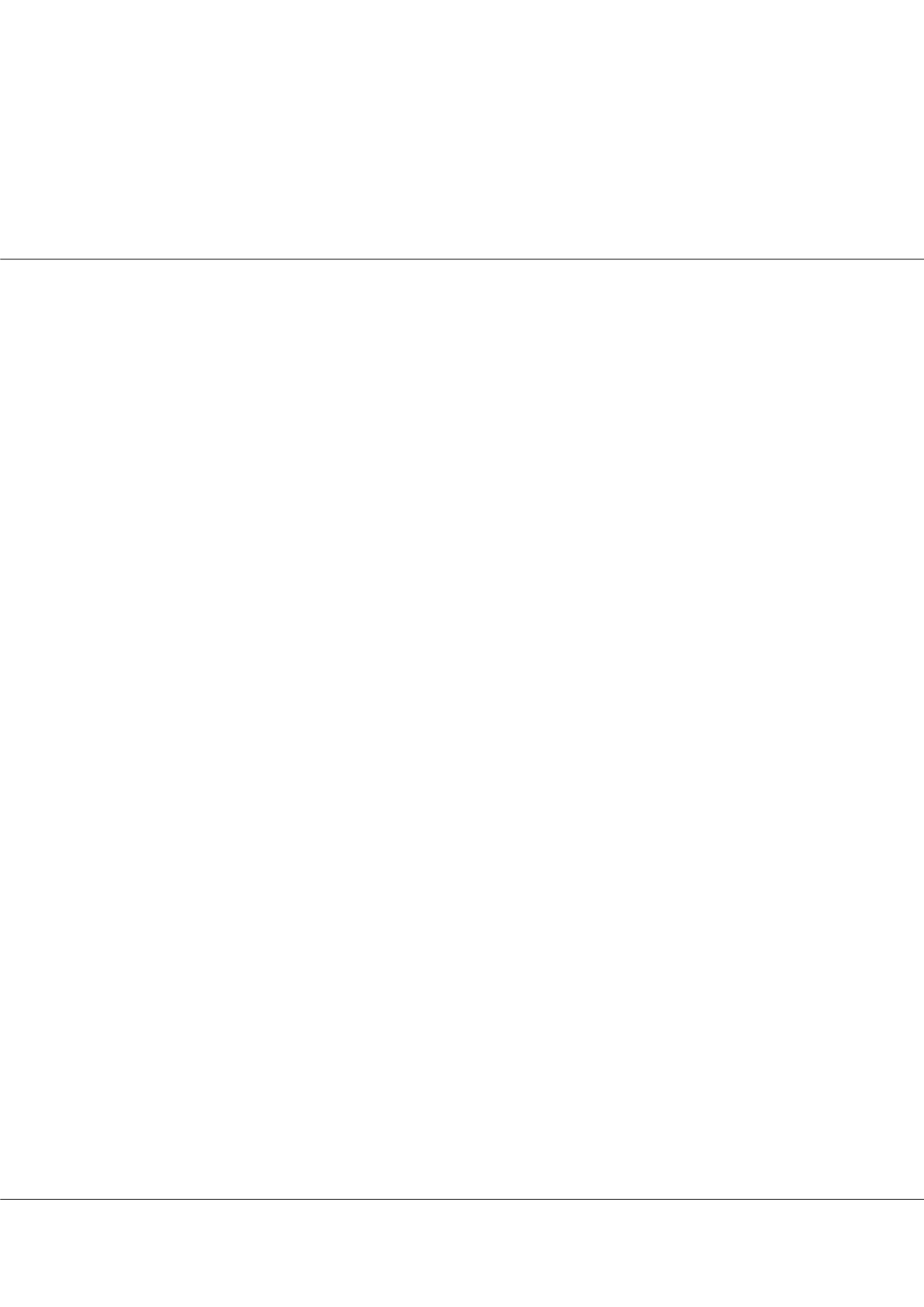
Page 155
conferenceseries
.com
Volume 6, Issue 4 (Suppl)
J Material Sci Eng, an open access journal
ISSN: 2169-0022
Materials Congress 2017
June 12-14, 2017
June 12-14, 2017 Rome, Italy
Materials Science and Engineering
9
th
World Congress on
J Material Sci Eng 2017, 6:4(Suppl)
DOI: 10.4172/2169-0022-C1-068
Functional surfaces – Development of innovative products
Aline Holder
1
and
Klaus Vissing
2
1
Festo AG & Co. KG, Germany
2
Fraunhofer Institute for Manufacturing Technology - IFAM, Germany
S
urfaces and their properties are playing an increasingly important role in industry application. In general, materials are used
according to their property requirements such as elasticity, strength, heat resistance or tomeet other requirements such as corrosion
resistance. However, traditional surfaces are often not able to meet the ever increasing demands of today´s applications in automotive,
textile, medical and food industry. Thus, in recent years, advances have been made using functional coatings to exceed limitations of
material to make surfaces more attractive for specific industry applications. Hygienic and efficient automation technologies are key
aspects for a successful production process for example in the food and beverage industry. Requirements regarding the cleanability
and durability of surfaces that are in food contact are important factors. The approach of this study was to design functional surfaces
with easy to clean and/ or self-cleaning coatings that enable automation components to be easily or less cleaned. For coating procedure
physical vapor deposition was carried out in order to facilitate separation of the vaporized coating material to the substrate. Substrates
used are aluminum, stainless steel and plastics for example polyamide or polyethylene. Analytical description of surface characteristics
was performed using scanning electron microscopy, contact angel and roughness. Different surfaces were successfully coated with
easy to clean coatings and characterized analytically. In addition, coating of automation components consisting of different materials
was realized and coating adhesion was improved. First application tests showed a clear improvement of material properties relating
to chemical resistance and cleanability compared to today’s standard materials used.
Aline.Holder@festo.comCoupled thermal-mechanical simulation for continuous casting of lightweight alloys
Amir M Horr, Johannes Kronsteiner, Stefan Scheiblhofer, Christian Müllshttäter
and
Stephan Ucsnik
Austrian Institute of Technology, Austria
T
he numerical simulations of industrial continuous and semi-continuous casting process for lightweight alloys have been used
extensively to investigate the optimization of casting billets with high quality within relatively low operating cost and energy. The
thermal evolution during the casting process and the industrial trend to control the rate of heat transfer coefficient (HTC) during
both start-up and during-casting phases has been broadly studied. However, the estimation of HTC values during air, contact and
water/oil cooling and the implementation of thermal and mechanical phenomena during casting process have relatively received
little attention. The development of advanced numerical techniques (including multi-physical and evolving domain techniques) for
thorough process simulation of the melt flow, heat transfer and evolution of stress/strain and damage during casting process has
promoted many new opportunities. However, smarter and broader improvements are needed to capture the underlying physical and
chemical phenomena including multi-physical transient fluid-thermal-mechanical coupling and heat-transfer changes during the
process. For the starting-cast condition where most of mechanical cracking and damage are initiating, there have been many efforts to
control mechanical defects by optimizing casting recipes. The concerns about cast billet quality and the minimization of hot tearing,
cold cracking, and shrinkage dimensional control are part of casting quality control. Within this framework, the cooling system
numerical simulation including its fluid flow and its characteristics (turbulence, free surface boundaries, etc.) heat transfer have to be
modeled. In the research work herein, parallel experimental-numerical studies of coupled transient thermal-mechanical phenomena
including HTC estimation using empirical and reverse analyses are presented. The phase change modeling during semi-continuous
casting process including liquid and solid interface, and also implementation of dynamic HTC curves are also considered. One of
the main contributions of this paper is to show the applicability and reliability of newly developed coupled thermal-mechanical
numerical simulation approach for the optimization of continuous and semi-continuous casting process.
amir.horr@ait.ac.at