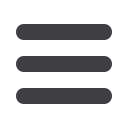
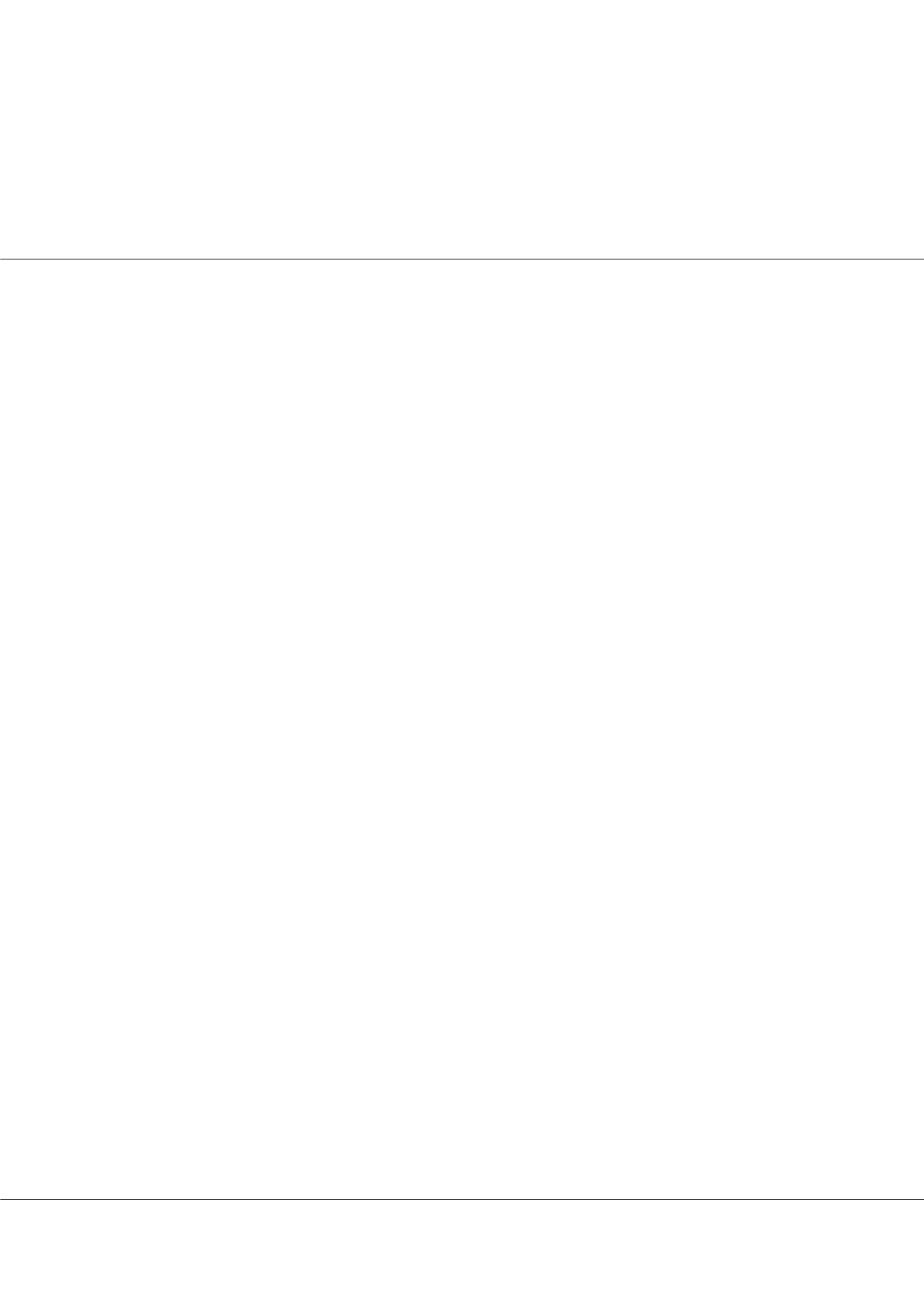
Page 42
Notes:
conferenceseries
.com
October 27-29, 2016 Rome, Italy
15
th
International Conference on
Food Processing & Technology
Volume 7, Issue 12 (Suppl)
J Food Process Technol 2016
ISSN: 2157-7110 JFPT, an open access journal
Food Technology 2016
October 27-29, 2016
Waste heat recovery in food & drink industry
Sanjay Mukherjee, Abhishek Asthana
and
Martin Howarth
Sheffield Hallam University, UK
M
ost baking processes in the food manufacturing sector involve use of gas-fired ovens. Only about one-third of the total
energy used in these ovens adds value to the final product. The remaining two-thirds is discharged with the exhaust gases
at 150-250
o
C and thus represents an opportunity for heat recovery. However, the low temperature range, fouling and presence of
corrosive materials in the exhaust streams make heat recovery technically challenging and uneconomical. The existing low grade heat
recovery technolgies mostly use gas to liquid heat transfer to produce hot water for use in other areas of the manufacturing plant.
The performance of these systems is governed by hot water demand in the factory and is therefore not recommended if there are
frequent fluctuations in demand or if a more efficient technology, such as combined heat and power, is already in place. This study
involves design, manufacturing and testing of a novel low-temperature gas to gas heat recovery system using an array of heat pipe heat
exchangers, for industrial-scale baking ovens at a large confectionary manufacturing plant. Unlike gas to liquid heat transfer, a gas to
gas heat transfer system provides direct savings in oven fuel consumption, independent of the hot water and other energy demands
elsewhere in the plant. The heat recovery potential of the system is estimated using a thermodynamic model developed based on
energy and mass balance for the ovens. The design enables recovery of up to 50% of the energy available through the exhaust stack,
increasing the energy efficiency of the overall process to 60% and reducing food manufacturing costs by one third.
Biography
Sanjay Mukherjee joined Sheffield Hallam University in 2015 as a Research Associate in an Innovate UK funded project on waste heat recovery. He obtained
his PhD in Carbon Capture and Storage from University of Surrey, UK. He has worked in collaboration with leading research groups from Cambridge University,
Imperial College and Tsinghua University for an EPSRC funded project and has published papers in reputed journals. He has also worked as a Technical Consultant
for Office of Carbon Capture and Storage at Department of Energy and Climate Change (DECC), London after PhD.
s.mukherjee@shu.ac.ukSanjay Mukherjee et al., J Food Process Technol 2016, 7:12 (Suppl)
http://dx.doi.org/10.4172/2157-7110.C1.056