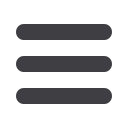
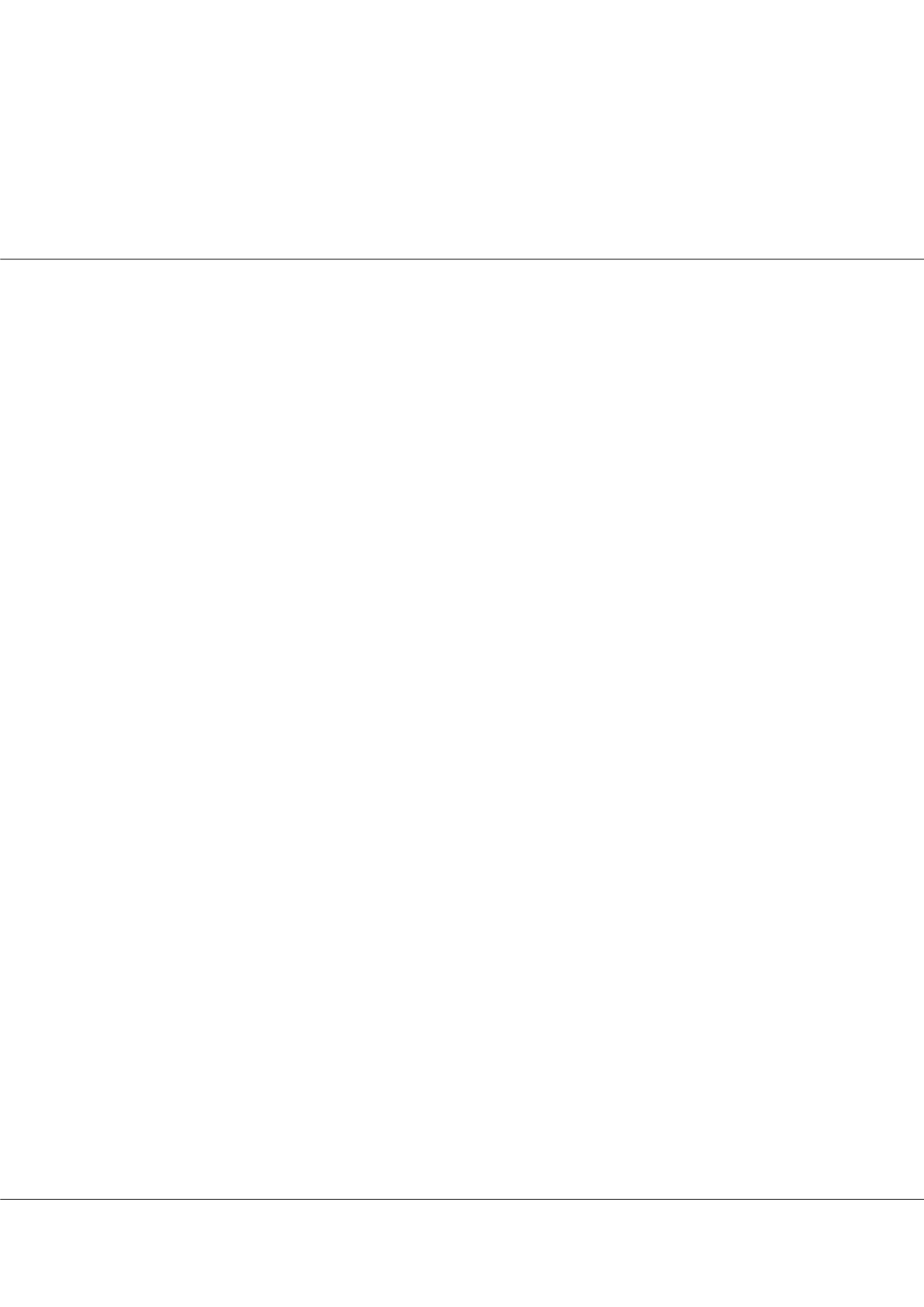
Page 96
conferenceseries
.com
Joint Conference
July 17-18, 2017 Chicago, USA
International Conference on
DIAMOND AND CARBON MATERIALS & GRAPHENE AND SEMICONDUCTORS
Volume 6, Issue 6 (Suppl)
J Material Sci Eng, an open access journal
ISSN: 2169-0022
Diamond and Carbon 2017 & Graphene 2017
July 17-18, 2017
J Material Sci Eng 2017, 6:6(Suppl)
DOI: 10.4172/2169-0022-C1-077
Abrasive superhard composite materials based on diamond and cubic boron nitride structured by
nanocarbon binder at subatmospheric pressures intended for grinding and polishing tools and pastes
Poltoratskyi V.G
V.Bakul Institute of Superhard Materials, Ukraine
T
he results of work on the development of abrasive superhard composite materials based on diamond and cubic boron
nitride due to structuring the powder material by carbon binder at subatmospheric pressures are presented in the
paper. The use of new material results in increase of efficiency of grinding and polishing tools and pastes based on superhard
materials. It was first found that during the formation of the carbon binder from carbon-containing gas (CH
4
) on the
surface of particles in the diamond and cubic boron nitride compacts the filamentous carbon particles (whiskers), which bind
the particles together, are formed under such conditions: temperature gas flow rate – 3.1 10-5 - 4.7 10-5 m3/s. It was
ascertained that the formation in the structure of the compacts, specifically in space between the grains of initial SHM, globular
and filamentous carbon results in increased thermal stability of the compacts, the strength of the compacts is not decreased
at heating to 1474 K in argon. It was found that just addition to initial powders the micron powders of diamond or cBN of
grain sizes: 3/2, 2/1, 1/0 results in increase of strength of composite by 20 % due to decrease of pore size of the composite.
Experimental-industrial test showed advantages of the composite materials, a increase of durability of the grinding tool by 1.5
-3.0 times and a increase of abrasive abilityof pastes by 1.3 - 1.5 times.
vg.poltoratsky@gmail.comThe effect of carbon materials on the performance of a direct carbon fuel cell with molten
hydroxide electrolyte
Xiaofeng Li
and
Yanfang Gao
Inner Mongolia University of Technology, P.R. China
The direct carbon fuel cells (DCFCs) belong to new generation of energy conversion devices that are characterized by much
higher efficiencies and lower emission of pollutants than conventional coal-fired power plants.[1]Over the past several
decades fuel cell technologies have been treated as promising candidates for various utility applications.Today fuel cells are
still considered an environmentally friendly and highly efficient electricity generating systems and extensive research has been
conducted worldwide to improve this technology.The direct carbon fuel cell (DCFC) is a unique type of fuel cell able to convert
efficiently the chemical energy of solid carbonaceous fuels directly into electricity without the combustion of the fuels. The
theoretical maximum efficiency of carbon conversion in the DCFC is 100%,but practical efficiencies have been demonstrated at
roughly 80% [2]. The direct carbon fuel cell (DCFC) can be used to generate electricity directly from almost any carbonaceous
fuel, including carbonaceous waste materials, graphite, charcoals,carbon blacks, carbon fiber, and coals.[3]Here we focused
different carbon materials such as commercial graphite,carbon black,commercial hard coal,biochar and active carbon,thus can
find a better material for the improvement of the molten hydroxide direct carbon fuel cell. Biomass carbon sources with an
inter-connected multirole pore or beneficial element through a green route are a new generation of electrode, which is rapidly
expanding research area. The extraordinary synthetic approach presented here opens the door of green chemistry for biomass-
based the direct carbon fuel cell, which considers various pore geometries and dipping of element to design electrode
materials with improved battery performance. Above all, the routes used to synthesize this carbon-based electrode are readily
scalable to industrial levels.
yf_gao@imut.edu.cn