Reduction of Toxic Cr6+ Ions Using Fluidized Bed of Iron Particles
Semary MM1, Zatout AA2, Nosier SA2 and Mansour MS2*
1Ministry of Electricity and Water, Kuwait
2Chemical Engineering Department, Faculty of Engineering, Alexandria University, Alexandria, Egypt
- *Corresponding Author:
- Mansour MS
Chemical Engineering Department
Faculty of Engineering
Alexandria University
Alexandria, Egypt
Tel: 201-223-821-047
E-mail: mansourms@alexu.edu.eg
Received date: February 06, 2016; Accepted date: February 16, 2016; Published date: February 21, 2016
Citation: Semary MM, Zatout AA, Nosier SA, Mansour MS (2016) Reduction of Toxic Cr6+ Ions Using Fluidized Bed of Iron Particles. Ind Chem 2:116. doi:10.4172/2469-9764.1000116
Copyright: © 2016 Semary MM, et al. This is an open-access article distributed under the terms of the Creative Commons Attribution License, which permits unrestricted use, distribution, and reproduction in any medium, provided the original author and source are credited.
Visit for more related articles at Industrial Chemistry
Abstract
The kinetics of the cementation of chromium ions from potassium dichromate solution onto fluidized bed of iron particles were investigated in a stirred tank reactor. Variables studied were physical properties of the solution, stirring speed (rpm) and temperature. The rate of cementation was found to increase with increasing rpm and concentration. The rate of cementation was expressed in terms of the liquid–solid mass transfer coefficient (k). The data were correlated by the equation:
Sh=0.52 Sc0.33Re0.4957
The high rates of mass transfer obtained in this work and the high area per unit volume of fluidized bed of iron qualify them for building high space time reactors suitable for purification of hydrometallurgical leach liquors and removal of heavy metal from waste water by cementation.
Keywords
Chromium ions; Fluidized bed; Heavy metal; Waste water; Biometallic; Electroplating
Introduction
Hexavalent and trivalent chromium are the stable form of presence of chromium in water. Cr(IV) is known to be carcinogenic and toxic; thus causing health problems e.g., vomiting, severe diarrhea, pulmonary congestions and liver damage. Whereas Cr (III) is less toxic [1,2] Cr(III) is essential in human nutrition (especially in glucose metabolism) [3-6]. Chromium ions are non-degradable and can accumulate in living tissue. Although some heavy metals in low dosage are essential micronutrients for plants and animals, in higher doses they can detrimentally affect the health of most living organisms [7-9].
From economical aspect, the advantages of chromium applications in different industries [10,11], such as the production of stainless steel, in electroplating, refractory industry, tanning of leather, pigment and chemical industry, etc., contrast with its negative external effects as a hazardous pollutant. Numerous soils, waste sites, groundwater, and surface waters are contaminated with anthropogenic Cr(VI) [12-14].
In general, chromium (VI) is removed from waste water by various methods such as adsorption [15-32] biometallic as high efficiency removing method [33], Coagulation precipitation [34], Electrocoagulation [35-38], membrane [39-45], sorption [46-56], Step-by- step deposition and extraction technique [57], reduction [58-60].
Cementation is one of the oldest and simplest hydrometallurgical processes, which has been used as a means of extracting metals from solution. Only in the past 20 years, considerable attention has been paid to two main industrial applications of cementation. The first involves the recovery of metals from leach solution [57-59] and the second is concerned with the purification of electrolyte solutions to remove metals which are more electropositive than the metal to be deposited, e.g., Cu, Co, Ni, Cd from ZnSO4 electrolyte [61-64].
Experimental Part
Materials and methods
All chemical reagents [K2Cr2O7, H2SO4] were in analytical reagent grade. Stock solutions of 0.001- 0.002- 0.003 and 0.004 M of K2Cr2O7 were prepared by dissolving AR grade chemicals in distilled water. Iron particles were etched in dilute HCl to remove the oxide layer, washed with distilled water and dried before each run. The size of iron particles was between 1.0 and 0.8 mm (≅0.9 mm).
Apparatus: Figure 1 shows the experimental setup used in the present study. It consisted mainly baffled cylindrical container of volume 3/4 liter. The container is stirred with 4 Blade 45° pitched blade metal turbine coated with epoxy. The dimensions of the cylinder are as follows: J (baffles thickness)=1 cm, W (blade width)=1 cm, L (blade length)=1.25 cm, Da (Impeller diameter)=5 cm and E (Impeller height)=3 cm.
Figure 1: Apparatus used.
Procedure: Before each run 0.75 L of acidified potassium dichromate solution were introduced to the container. The rate of cementation of Cr6+ on the iron particles was determined by measuring the change in Cr6+ concentration with time. The time dependence of chromium concentration was monitored during cementation by withdrawing a sample of 5 cm3 at different time intervals for analysis by titration against standard ferrous ammonium sulfate (0.01N) in presence of sodium diphenylamine sulfonate as an indicator.
The solution viscosity and density needed for data correlation were determined experimentally by an Ostwald viscometer and a density bottle respectively [65], while the diffusivity of acidified potassium dichromate was obtained from the literature [66,67].
Results and Discussion
The mass transfer coefficient of the diffusion controlled cementation of chromium on zinc particles was obtained under different conditions from the potassium dichromate concentration-time data. Figure 2 show that the data fit the equation:
which upon integration yields;
where Co is the initial concentration of potassium dichromate, C is the concentration of potassium dichromate at time (t), Vs is the solution volume, A is the surface area of the iron particles in the bed, which was calculated in terms of particle diameter from the equation:
where: m=mass of iron particles; ρ=density of iron; dp=particle diameter. The mass transfer coefficient (K) was calculated from the slope of the straight line obtained by plotting ln(Co/C) versus time typical figure is shown in Figure 2.
Figure 2: Typical plot of ln (Co/C) Vs time at different rpm.
To correlate the present mass transfer data, the method of dimensional analysis was used. The present data could be correlated by the functional equation:
K=f(ρ, μ, D, V, di, dp) Where: K=mass transfer coefficient; ρ=density of the solution; μ=viscosity of the solution; D=diffusivity of chromium ions; V=impeller linear velocity, dp=iron particle diameter, di=impeller diameter.
Dimensional analysis leads to writing of the previous equation in the form of 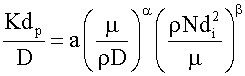
The exponent β and the constant (a) were determined using the experimental data. Following previous theoretical and experimental studies in mass transfer [68,69], the exponent 0.33 was used for α. Figure 4 Shows the effect of impeller speed on the mass transfer coefficient, Figure 5 shows the effect of Re on Sh at different Sc and the equation).
Figure 3: Effect of temperature on mass transfer coefficient.
Figure 4: Effect of impeller speed on mass transfer coefficient.
Figure 5: Log (Sh) versus log (Re) for different Sc.
Figure 5 shows the present data for the conditions: 954.899<Sc<1198.3024; 2.16 × 104<Re<5.97 × 104 fit the equation:
Sh=0.52 Sc0.33Re0.4957
The increase in the mass transfer coefficient of Cr6+ cementation on iron particles with increasing impeller rotation speed confirms the diffusion controlled nature of cementation reaction [70,71]. Figure 3 also shows that the activation energy is 4.5 kcal/mole <5 kcal/mole thus insuring the diffusion effect. The increase in the rate of mass transfer with increasing impeller speed is attributed to the increase in the intensity of turbulence in the agitated vessel which reduces the liquid phase diffusion layer thickness around the iron particles with a consequent increase in the mass transfer coefficient, which is related to the diffusion layer thickness (δ) by the equation [68,69]

Conclusion
The use of fluidized bed of iron to reduce Cr6+ to Cr3+ which is non-toxic found to be diffusion controlled. The using of the powder increase the surface area and thus the rate of reduction i.e., it offers high space time yield cementation reactor suitable for reduction of Cr6+. The present mass transfer equation can be used for fluidized (suspended) bed reactor.
References
- Eary LE, Rai D (1988) Chromate removal from aqueous wastes by reduction with ferrous ion.Environ Sci Technol 22: 972-977.
- Yurik TK, Pikaev AK (1999) Radiolysis of weakly acidic and neutral aqueous solutions of hexavalent chromium ions. High Energy Chem 33: 208-212.
- Katz SA, Salem H (1995) The Biological and Environmental Chemistry of Chromium. VCH Publishers 15: 337.
- Nriagu JO, Nieboer E (1988) Chromium in the Natural and Human Environments. Wiley, General Environmental Chemistry.p: 571.
- Mertz W, Murti CRK, Bingheng C, Gopalan HNB, MassoudA, et al.(1988) Chromium. World Health Organization: Geneva.
- Perlman GD, Berman L, Leann K, Bing L (2012) Agency for Toxic Substances and Disease Registry Brownfields/ land-reuse site tool. J Environ Health 75: 30-34.
- ShrivastavaR, Upreti RK, Chaturvedi UC (2003) Various cells of the immune system and intestine differ in their capacity to reduce hexavalent chromium.FEMS Immunol Med Microbiol 38: 65-70.
- Yemane M, Chandravanshi BS, Wondimu T (2008) Levels of essential and nonessential metals in leaves of the tea plant (Camellia sinensis L.) and soil of Wushwush farms, Ethiopia. Food Chem 107:1236-1243.
- PécouE, Maass A, Remenik D, Briche J, Gonzalez M (2006) A mathematical model for copper homeostasis in Enterococcus hirae. Math Biosci 203: 222-239.
- Katz SA, Salem H (1988) The Biological and Environmental Chemistry of Chromium. VCH: New York, USA.
- Nriagu JO, Nieboer E (1988) Chromium in the Natural and Human Environments. Advances in Environmental Science and Technology 20: 572.
- Calder LM, Nriagu JO, Nieboer E (1988) In Chromium in the Natural and Human Environments. Wiley & Sons.pp: 215-229.
- Palmer CD, Wittbrodt PR (1991) Processes affecting the remediation of chromium-contaminated sites. Environ Health Perspect 92: 25-40.
- Buerge I, Hug SJ (1997) Kinetics and pH Dependence of Chromium (VI) Reduction by Iron (II). Environ SciTechnol 31: 1426-1432.
- Hokkanen S, Bhatnagar A, Repo E, Lou S, Sillanpää M (2016) Calcium hydroxyapatite microfibrillated cellulose composite as a potential adsorbent for the removal of Cr(VI) from aqueous solution. Chemical Engineering Journal 283: 445-452.
- Dudu TE, Sahiner M, Alpaslan D, Demirci S, Aktas N (2015) Removal of As(V), Cr(III) and Cr(VI) from aqueous environments by poly(acrylonitril-co-acrylamidopropyl-trimethyl ammonium chloride)-based hydrogels. J Environ Manage 161: 243-251.
- Zhang H, Huang F, Liu DL, Shi P (2015) Highly efficient removal of Cr(VI) from wastewater via adsorption with novel magnetic Fe3O4@C@MgAl-layered double-hydroxide. Chinese Chemical Letters 26: 1137-1143.
- Sugashini S, Meera KM, Begum S, Ramalingam A (2015) Removal of Cr(VI) ions using Fe-loaded chitosan carbonized rice husk composite beads (Fe-CCRCB): Experiment and quantum chemical calculations. Journal of Molecular Liquids 208: 380-387.
- Li F, Chen Y, Huang H, Cao W,Li T (2015) Removal of rhodamine B and Cr(VI) from aqueous solutions by a polyoxometalate adsorbent. Chemical Engineering Research and Design 100: 192-202.
- Wang X, Zhang Y, Li J, Zhang G, Li X (2015) Enhance Cr(VI) removal by quaternary amine-anchoring activated carbons. Journal of the Taiwan Institute of Chemical Engineers 58: 434-440.
- Rodrigues LA, Sakane KK, Simonetti EAN, Thim GP (2015) Cr total removal in aqueous solution by PHENOTAN AP based tannin gel (TFC). Journal of Environmental Chemical Engineering 3: 725-733.
- Mandal S, Mahapatra SS, Patel RK (2015) Enhanced removal of Cr(VI) by cerium oxide polyaniline composite: Optimization and modeling approach using response surface methodology and artificial neural networks. Journal of Environmental Chemical Engineering 3: 870-885.
- Mukhopadhyay P, Chakraborty R, Chakraborty M, Mitra A (2015) Infrared irradiation aided fabrication of Mn impregnated-natural bone adsorbent: Efficacy evaluation in aqueous Cr(VI) removal. Journal of Water Process Engineering 6: 32-41.
- Jia Z, Qin Q, Liu J, Shi H, Zhang X, et al. (2015) The synthesis of hierarchical ZnFe2O4 architecture and their application for Cr(VI) adsorption removal from aqueous solution. Superlattices and Microstructures 82: 174-187.
- Sugashini S, Begum KMMS (2015) Preparation of activated carbon from carbonized rice husk by ozone activation for Cr(VI) removal. New Carbon Materials 30: 252-261.
- Zhao Y, Qi W, Chen G, Ji M, Zhang Z (2015) Behavior of Cr(VI) removal from wastewater by adsorption onto HCl activated Akadama clay. Journal of the Taiwan Institute of Chemical Engineers 50: 190-197.
- Dubey R, Bajpai J, Bajpai AK (2015) Green synthesis of graphene sand composite (GSC) as novel adsorbent for efficient removal of Cr (VI) ions from aqueous solution. Journal of Water Process Engineering 5: 83-94.
- Fida H, Guo S, Zhang G (2015) Preparation and characterization of bifunctional Ti-Fe kaolinite composite for Cr(VI) removal. J Colloid Interface Sci 442: 30-38.
- Setshedi KZ, Bhaumik M, Onyango MS, Maity A (2015) High-performance towards Cr(VI) removal using multi-active sites of polypyrrole–graphene oxide nanocomposites: Batch and column studies. Chemical Engineering Journal 262: 921-931.
- Sun X, Yang L, Li Q, Liu Z, Dong T, et al. (2015) Polyethylenimine-functionalized poly(vinyl alcohol) magnetic microspheres as a novel adsorbent for rapid removal of Cr(VI) from aqueous solution. Chemical Engineering Journal 262: 101-108.
- Wang H, Yuan X, Wu Y, Chen X, Leng L, et al. (2015) Facile synthesis of polypyrrole decorated reduced graphene oxide–Fe3O4 magnetic composites and its application for the Cr(VI) removal. Chemical Engineering Journal 262: 597-606.
- Karthik R, Meenakshi S (2015) Removal of Cr(VI) ions by adsorption onto sodium alginate-polyanilinenanofibers. Int J BiolMacromol 72: 711-717.
- Fu F, Cheng Z, Dionysiou DD, Tang B (2015) Fe/Al bimetallic particles for the fast and highly efficient removal of Cr(VI) over a wide pH range: Performance and mechanism. J Hazard Mater 298: 261-269.
- Golbaz S, Jafari AJ, Rafiee M, Kalantary RR (2014) Separate and simultaneous removal of phenol, chromium, and cyanide from aqueous solution by coagulation/precipitation: Mechanisms and theory. Chemical Engineering Journal 253: 251-257.
- El-Taweel YA, Nassef EM, Elkheriany I, Sayed D (2015) Removal of Cr(VI) ions from waste water by electrocoagulation using iron electrode. Egyptian Journal of Petroleum 24: 183-192.
- Chen Q, Fu R, Fang X, Cai W, Wang Y, Cheng S (2015) Cr-methanol fuel cell for efficient Cr(VI) removal and high power production. Applied Energy 138: 31-35.
- Zewail TM, Yousef NS (2014) Chromium ions (Cr6+ & Cr3+) removal from synthetic wastewater by electrocoagulation using vertical expanded Fe anode. Journal of Electroanalytical Chemistry 735: 123-128.
- Hamdan SS, El-Naas MH (2014) Characterization of the removal of Chromium (VI) from groundwater by electrocoagulation. Journal of Industrial and Engineering Chemistry 20: 2775-2781.
- Kaya A, Onac C, Alpoguz HK, Yilmaz A, Necip A (2016) Removal of Cr(VI) through calixarene based polymer inclusion membrane from chrome plating bath water. Chemical Engineering Journal 283: 141-149.
- Dehghani MH, Taher MM, Bajpai AK, Heibati B, Tyagi I, et al. (2015) Removal of noxious Cr (VI) ions using single-walled carbon nanotubes and multi-walled carbon nanotubes. Chemical Engineering Journal 279: 344-352.
- Yao Z, Li Y, Cui Y, Zheng K, Zhu B, et al. (2015) Tertiary amine block copolymer containing ultrafiltration membrane with pH-dependent macromolecule sieving and Cr(VI) removal properties. Desalination 355: 91-98.
- Doke SM, Yadav GD (2014) Process efficacy and novelty of titania membrane prepared by polymeric sol–gel method in removal of chromium(VI) by surfactant enhanced microfiltration. Chemical Engineering Journal 255: 483-491.
- Chakraborty S, Dasgupta J, Farooq U, Sikder J, Drioli E, et al. (2014) Experimental analysis, modeling and optimization of chromium (VI) removal from aqueous solutions by polymer-enhanced ultrafiltration. Journal of Membrane Science 456: 139-154.
- Yang R, Aubrecht KB, Ma H, Wang R, Grubbs RB, et al. (2014) Thiol-modified cellulose nanofibrous composite membranes for chromium (VI) and lead (II) adsorption. Polymer 55: 1167-1176.
- Bhattacharya M, Dutta SK, Sikder J, Mandal MK (2014) Computational and experimental study of chromium (VI) removal in direct contact membrane distillation. Journal of Membrane Science 450: 447-456.
- Deravanesiyan M, Beheshti M, Malekpour A (2015) The removal of Cr (III) and Co (II) ions from aqueous solution by two mechanisms using a new sorbent (alumina nanoparticles immobilized zeolite) — Equilibrium, kinetic and thermodynamic studies. Journal of Molecular Liquids 209: 246-257.
- Arris S, Lehocine MB, Meniai AH (2014) Sorption study of chromium sorption from wastewater using cereal by-products. International Journal of Hydrogen Energy
- Jayakumar R, Rajasimman M, Karthikeyan C (2014) Sorption of hexavalent chromium from aqueous solution using marine green algae Halimedagracilis: Optimization, equilibrium, kinetic, thermodynamic and desorption studies. Journal of Environmental Chemical Engineering 2: 1261-1274.
- Wang Y, Fang Z, Liang B, Pokeung TE (2014) Remediation of hexavalent chromium contaminated soil by stabilized nanoscale zero-valent iron prepared from steel pickling waste liquor. Chemical Engineering Journal 247: 283-290.
- Vieira RS, Meneghetti E, Baroni P, Guibal E, Cruz VMG, et al. (2014) Chromium removal on chitosan-based sorbents – An EXAFS/XANES investigation of mechanism. Materials Chemistry and Physics146: 412-417.
- Oladoja NA, Ololade IA, Alimi OA, Akinnifesi TA, Olaremu GA (2013) Iron incorporated rice husk silica as a sorbent for hexavalent chromium attenuation in aqueous system. Chemical Engineering Research and Design 91: 2691-2702.
- Gonzalez MR, Pereyra AM, Sánchez RMT, Basaldella EI (2013) Chromium removal by zeolite-rich materials obtained from an exhausted FCC catalyst: Influence of chromium incorporation on the sorbent structure. Journal of Colloid and Interface Science 408: 21-24.
- Zhao Y, Zhang J, Zheng C (2013) Release and removal using sorbents of chromium from a high-Cr lignite in Shenbei coalfield China. Fuel 109: 86-93.
- Sillerova H, Komarek M, Chrastny V, Novak M, Vanek A, Drabek O, et al. (2013) Brewers draff as a new low-cost sorbent for chromium (VI): comparison with other biosorbents. J Colloid Interface Sci 396: 227-233.
- Escudero C, Fiol N, Villaescusa I, Bollinger J (2013) Effect of chromium speciation on its sorption mechanism onto grape stalks entrapped into alginate beads. Arabian Journal of Chemistry.
- Gherasim C, Bourceanu G (2013) Removal of chromium(VI) from aqueous solutions using a polyvinyl-chloride inclusion membrane: Experimental study and modeling. Chemical Engineering Journal 220: 24-34.
- Mahmoud ME, Obada MK, Kassem TS (2013) Removal and speciation of chromium by static step-by-step deposition and extraction technique. Chemical Engineering Journal 230: 210-219.
- Kantar C, Ari C, Keskin S (2015) Comparison of different chelating agents to enhance reductive Cr(VI) removal by pyrite treatment procedure. Water Res 76: 66-75.
- Kantar C, Ari C, Keskin S, Dogaroglu ZG, Karadeniz A, et al. (2015) Cr(VI) removal from aqueous systems using pyrite as the reducing agent: batch, spectroscopic and column experiments. J Contam Hydrol 174: 28-38.
- Sun L, Yuan Z, Gong W, Zhang L, Xu Z, et al. (2015) The mechanism study of trace Cr(VI) removal from water using Fe0 nanorods modified with chitosan in porous anodic alumina. Applied Surface Science 328: 606-613.
- Ettel V (1981) Volume 2. Plenum, New York, USA.
- Bro P, Lang KC (1989) Estimating Cancer mortality. J Environ Sci Technol 23: 925-930.
- Genon G, Parti P (1983) J Gaglia Chim Ind (Milan) 65: 79.
- Hendrickson DJ, Benjamin MM, Ferguson JF, GoebelL J (1984) Removal of Silver and Mercury from Spent COD Test Solutions.J Water Pollution Control Federation 56:468-473.
- Findlay A, Kitchener JA (1965) Practical physical chemistry. Longmans, London.
- Gregory DP, Riddiford AC (1960) Dissolution of copper in sulfuric acid solutions. Journal of the Electrochemical Society.pp: 950-956.
- Iadicicco N, Paduano L, Vitagliano V (1996) Diffusion coefficients for the system potassium chromate – water at 25°C. J Chem Eng Data 41: 529-533.
- McCabe WL, Smith JC, Harriot P (1985) Unit operations of chemical engineering. McGraw Hill Inc.
- Geankoplis CJ (1978) Transport process and Unit operations.Allyn and Bacon Inc., London.
- Power GP, Ritchie IM (1975) Modern Aspects of Electrochemistry. Prentice-Hall, New York. p: 199.
- Agrawal RD (1988) Metals and Fuels. J of Mines, p: 138.
--